Wood pellet extruder machines play a crucial role in the biomass industry by transforming raw wood materials into high-density pellets that serve various purposes, including energy generation, animal bedding, and soil enhancement. Grasping the working principle of these machines is essential for optimizing their efficiency and producing high-quality pellets. This article delves into the primary components and processes involved in the operation of a wood pellet extruder machine.
1. Raw Material Preparation
Before the extrusion process begins, it is essential to prepare the raw materials properly. This preparation includes several steps:
- Material Selection: Common raw materials include wood chips, sawdust, and agricultural residues. The choice of material significantly influences the quality of the final pellets.
- Grinding: Raw materials are ground into smaller particles using a hammer mill or similar equipment. This step is critical as smaller particle sizes enhance the efficiency of the extrusion process and improve pellet quality.
- Drying: Maintaining the correct moisture content of the raw materials is vital for successful pellet production. Typically, the moisture content should range between 10% and 15%. Excess moisture can impede the extrusion process, while insufficient moisture can result in poor pellet quality. A dryer is often employed to achieve the desired moisture level.
2. Feeding System
After the raw materials are prepared, they are fed into the wood pellet extruder machine through a feed hopper:
- Feed Hopper: The feed hopper is designed to hold and dispense raw materials into the extruder, ensuring a consistent flow that prevents blockages and facilitates smooth machine operation.
- Screw Feeder: A screw feeder may be used to transport the raw materials from the hopper to the extruder, regulating the feed rate and ensuring a steady supply of material.
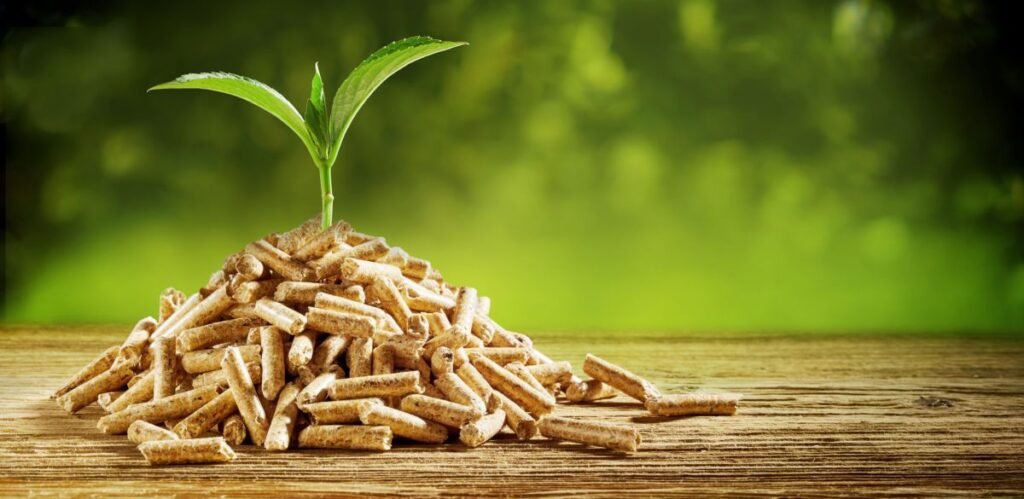
3. Extrusion Process
The extrusion process is the primary function of the wood pellet extruder machine and consists of several key components and steps:
- Extruder Barrel: Raw materials enter the extruder barrel, where they experience high pressure and temperature. The barrel is typically heated to soften the lignin in the wood, which acts as a natural binder during pelletization.
- Screw Shaft: The screw shaft rotates within the barrel, pushing the raw materials forward. As the materials progress through the barrel, they encounter increasing pressure and temperature due to the friction generated by the rotating screw.
- Compression and Heating: The combination of pressure and heat causes the lignin to soften and become sticky. This sticky lignin binds the wood fibers together, allowing the material to be shaped into pellets as it is forced through the die.
4. Pellet Die
The pellet die is a crucial component of the wood pellet extruder machine, determining the size and shape of the produced pellets:
- Die Design: The die consists of a metal plate with holes of specific diameters. The size of these holes determines the diameter of the pellets, which typically ranges from 6 mm to 12 mm, depending on the intended application.
- Pellet Formation: As the softened material passes through the die, it is formed into cylindrical pellets. The pressure from the screw shaft ensures that the pellets are dense and compact, essential for durability and combustion efficiency.
5. Cooling and Cutting
After the pellets are formed, they require cooling and cutting to the desired length:
- Cooling System: Newly extruded pellets are hot and soft due to the heat generated during extrusion. A cooling system, often a counter-flow cooler, is employed to lower the temperature of the pellets, solidifying them and preparing them for storage.
- Cutting Mechanism: A cutting mechanism, typically a knife or blade, is used to cut the long strands of pellets into uniform lengths. The pellet length can be adjusted based on user requirements.
6. Packaging
Once the pellets are cooled and cut, they are ready for packaging:
- Packing Machine: Finished pellets are usually packed into bags or bulk containers for storage and distribution. A packing machine ensures accurate weighing and sealing of bags, facilitating easy handling and transport.
7. Control and Automation Systems
Modern wood pellet extruder machines often incorporate advanced control and automation systems to enhance efficiency and monitor performance:
- PLC Control System: A programmable logic controller (PLC) manages and monitors the entire production process, allowing operators to adjust parameters such as temperature, pressure, and feed rate in real time.
- Sensors and Monitors: These devices track critical parameters, ensuring the production process remains efficient and consistent. They can provide alerts for maintenance needs or operational anomalies. (Related post: wood pellet maker for sale)
Conclusion
The operation of a wood pellet extruder machine involves several key steps, from raw material preparation to extrusion and final packaging. By understanding the components and processes involved, operators can optimize machine performance and ensure the production of high-quality pellets.
The growing demand for renewable energy sources and sustainable practices has made wood pellet extruder machines indispensable across various industries. As the biomass sector continues to expand, the importance of these machines will increase, contributing to a more sustainable future. By investing in high-quality wood pellet extruder machines and maintaining their components, businesses can improve production efficiency and meet the rising demand for biomass pellets.